SECTION 205-00: Driveline System — General Information
| 2014 Mustang Workshop Manual
|
GENERAL PROCEDURES
| Procedure revision date: 01/07/2013
|
Driveshaft Runout and Balancing
Special Tool(s)
 | Dial Indicator Gauge with Holding Fixture
100-002 (TOOL-4201-C) or equivalent
|
 | Mastertech® Series MTS 4000 Driveline Balance and NVH Analyzer (Vetronix)
257-00018 or equivalent
|
Driveshaft Inspection
NOTE:
Driveline vibration exhibits a higher frequency and lower amplitude than high-speed shake. Driveline vibration is directly related to the speed of the vehicle and is noticed at various speeds. Driveline vibration can be perceived as a tremor in the floorpan or heard as a rumble, hum or boom.
NOTE:
Refer to Specifications in this section for all runout specifications.
NOTE:
Do not make any adjustments before carrying out a road test. Do not change the tire pressure or the vehicle load.
Carry out a visual inspection of the vehicle. Operate the vehicle and verify the condition by reproducing it during the road test.
- The concern should be directly related to vehicle road speed, not affected by acceleration or deceleration or could not be reduced by coasting in NEUTRAL.
- With the vehicle in NEUTRAL, position it on a hoist. For additional information, refer to
Section 100-02
.
- The driveshaft should be kept at an angle equal to or close to the curb-weighted position. Use a twin-post hoist or a frame hoist with jackstands.
- Inspect the driveshaft for damage, undercoating or incorrectly seated U-joints. Rotate the driveshaft slowly by hand and feel for binding or end play in the U-joint trunnions. Remove the driveshaft. For additional information, refer to
Section 205-01
. Inspect the slip yoke splines for any galling, dirt, rust or incorrect lubrication. Clean the driveshaft or install new U-joints as necessary. Install a new driveshaft if damaged. After any corrections or new components are installed, recheck for the vibration at the road test speed.
- If the vibration is gone, test drive the vehicle.
- If the vibration persists or the driveshaft passes visual inspection, measure the driveshaft runout.
Driveshaft Runout
- Install the Dial Indicator Gauge with Holding Fixture. Rotate the driveshaft by turning the axle and measure the runout at the front, the center and the rear of the driveshaft.
- If the runout exceeds 1 mm (0.040 in) at the front or center, install a new driveshaft.
- If the front and center is within 1 mm (0.040 in), but the rear runout is not, index-mark the rear runout high point and proceed to Step 2.
- If the runout is within 1 mm (0.040 in) at all points, recheck for vibration at road test speed. If the vibration persists, balance the driveshaft. For additional information, refer to Driveshaft Balancing in this procedure.
NOTE:
Circular pinion flanges can be turned in 90 degree or one-fourth increments. Half-round pinion flanges are limited to 2 positions.
Index-mark the driveshaft to the pinion flange. Disconnect the driveshaft and rotate it 180 degrees. Reconnect the driveshaft. Recheck the runout at the rear of the driveshaft.
- If the runout is still over specification, mark the high point and proceed to Step 3.
- If the runout is within specification, check for the vibration at the road test speed. If the vibration is still present, balance the driveshaft. For additional information, refer to Driveshaft Balancing in this procedure.
- Excessive driveshaft runout can originate in the driveshaft itself or from the pinion flange. To find the source, compare the 2 high points previously determined.
- If the index marks are close together, within 25 mm (1 in), the driveshaft is eccentric. Install a new driveshaft.
- If the marks are on opposite sides of the driveshaft, 180 degrees apart, the slip yoke or pinion flange is responsible. Check the pinion flange runout. If the pinion flange runout exceeds specifications, a bent pinion is indicated.
- If the pinion flange and pinion runouts are within specifications, road test and check for the vibration at the road test speed. If the vibration persists, balance the driveshaft. For additional information, refer to Driveshaft Balancing in this procedure.
Driveshaft Balancing — Using the Mastertech® Series MTS 4000 Driveline Balance and NVH Analyzer (Vetronix)
All vehicles
- Install the Mastertech® Series MTS 4000 Driveline Balance and NVH Analyzer (Vetronix) to the vehicle.
- Working under the vehicle, install an accelerometer. The accelerometer can be attached and mounted near either the transmission or differential end of the driveshaft.
- Clean an area of the driveshaft and install the reflective tape, then install the photo-tachometer sensor. The sensor should be placed at approximately a 20-degree angle from perpendicular to the surface of the reflective tape. Make sure the sensor does not get moved during the balance procedure.
- Reflective tape.
- Photo-tachometer sensor.
- Using the Mastertech® Series MTS 4000 Driveline Balance and NVH Analyzer (Vetronix), run a driveshaft balance test with the driveshaft unmodified.
Vehicles with tapped pinion flanges
- Label the tapped holes in the pinion flange numerically, starting at the top hole as 1. Mark the remaining holes 2, 3 and 4. Label in the direction of rotation.
- Using the Mastertech® Series MTS 4000 Driveline Balance and NVH Analyzer (Vetronix), run a second test with the 12 mm (0.47 in) test weight set screw in the No. 1 hole, previously marked on the pinion flange.
- Remove the test weight, then install the weight combination directed by the Mastertech® Series MTS 4000 Driveline Balance and NVH Analyzer (Vetronix).
Vehicles without tapped pinion flanges
- Using the Mastertech® Series MTS 4000 Driveline Balance and NVH Analyzer (Vetronix), run a second test with a test weight. Using a metal band, secure the test weight to the end of the driveshaft. The weight should be placed at the end of the driveshaft tube, as close to the tube-to-yoke weld seam as possible. Mark the location of the test weight on the driveshaft, as shown in the figure below.
- Test weight.
- Tube-to-yoke weld seam.
- Driveshaft pinion flange.
- Select the test weight based on driveshaft size. Larger driveshafts use 10 g (0.353 oz). Smaller driveshafts use 5 g (0.176 oz).
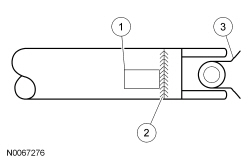
- Remove the test weight, then install the recommended weight at the position directed by the Mastertech® Series MTS 4000 Driveline Balance and NVH Analyzer (Vetronix). Using a metal band and epoxy, secure the test weight to the driveshaft, as shown in the figure below.
- Test weight.
- Measure in this direction.
- Driveshaft diameter.
- Directional rotation.
- Balance weight relative to test weight centerline.
- The results are displayed with respect to the location to where the test weight was placed.
All vehicles
- Using the Mastertech® Series MTS 4000 Driveline Balance and NVH Analyzer (Vetronix), run a third test to verify the repair.
Driveshaft Balancing — Hose Clamp Method
All vehicles
- Install 1 or 2 hose clamps on the driveshaft, near the rear. Position of the hose clamp head(s) can be determined through trial and error.
- Mark the rear of the driveshaft into 4 approximately equal sectors and number the marks 1 through 4. Install a hose clamp on the driveshaft with its head at position No. 1, as shown in the figure below. Check for vibration at road speed. Recheck with the clamp at each of the other positions to find the position that shows minimum vibration. If 2 adjacent positions show equal improvement, position the clamp head between them.
- If the vibration persists, add a second clamp at the same position and recheck for vibration.
- If no improvement is noted, rotate the clamps in opposite directions, equal distances from the best position determined in Step 2. Separate the clamp heads about 13 mm (1/2 in) and recheck for vibration at the road speed.
- Repeat the process with increasing separation until the best combination is found or the vibration is reduced to an acceptable level.
Vehicles with single piece driveshaft and automatic transmission
- If the transmission flange has endplay (up and down movement), repeat the process above on the driveshaft near the transmission flange.