SECTION 303-00: Engine System — General Information
| 2014 Mustang Workshop Manual
|
DIAGNOSIS AND TESTING
| Procedure revision date: 01/07/2013
|
Engine
Special Tool(s)
 | 12-Volt Master UV Diagnostic Inspection Kit
164-R0756 or equivalent (Leak Detector)
|
 | Dial Indicator Gauge with Holding Fixture
100-002 (TOOL-4201-C) or equivalent
|
 | EngineEAR
107-R2103 or equivalent
|
 | EngineEAR/ChassisEAR
107-R2102 or equivalent
|
 | Oil Pressure Gauge
303-088 (T73L-6600-A)
|
 | Vacuum/Pressure Tester
164-R0253 or equivalent
|
 | Vehicle Communication Module (VCM) and Integrated Diagnostic System (IDS)
software with appropriate hardware, or equivalent scan tool
|
Material
Item
| Specification
|
---|
Dye-Lite® Gasoline Engine Oil Leak Detection Dye
164-R3700 (Rotunda)
| —
|
Motorcraft® SAE 5W-20 Premium Synthetic Blend Motor Oil (US); Motorcraft® SAE 5W-20 Super Premium Motor Oil (Canada)
XO-5W20-QSP (US); CXO-5W20-LSP12 (Canada)
| WSS-M2C945-A
|
Aceite para motor SAE 5W-30 de mezcla sintética Motorcraft® Premium (EE. UU.);Aceite para motor SAE 5W-30 Motorcraft® Super Premium (Canadá)
XO-5W30-QSP (EE. UU.); CXO-5W30-LSP12 (Canadá)
| WSS-M2C946-A
|
Motorcraft® SAE 5W-50 Full Synthetic Motor Oil
XO-5W50-QGT or equivalent
| WSS-M2C931-B
|
There are 2 diagnostic paths that can be followed depending on the type of engine concern. Carry out Inspection and Verification — Engine Performance or Inspection and Verification — Engine NVH.
Inspection and Verification — Engine Performance
- Verify the customer concern by operating the engine to duplicate the condition.
- Visually inspect for obvious signs of mechanical damage. Refer to the following chart.
Visual Inspection Chart
Mechanical
|
---|
- Engine coolant leaks
- Engine oil leaks
- Fuel leaks
- Damaged or severely worn parts
- Loose mounting bolts, studs and nuts
|
- If the inspection reveals obvious concerns that can be readily identified, repair as necessary.
NOTE:
Make sure to use the latest scan tool software release.
If the cause is not visually evident, connect the scan tool to the Data Link Connector (DLC).
NOTE:
The Vehicle Communication Module (VCM) LED prove out confirms power and ground from the
are provided to the
.
If the scan tool does not communicate with the
:
- check the
connection to the vehicle.
- check the scan tool connection to the
.
- refer to
Section 418-00
, No Power To The Scan Tool, to diagnose no power to the scan tool.
- If the scan tool does not communicate with the vehicle:
- verify the ignition key is in the ON position.
- verify the scan tool operation with a known good vehicle.
- Carry out the network test.
- If the scan tool responds with no communication for one or more modules, refer to
Section 418-00
.
- If the network test passes, retrieve and record Continuous Memory Diagnostic Trouble Codes (CMDTCs).
- Clear the
and carry out the self-test diagnostics for the PCM.
- If the DTCs retrieved are related to the concern, refer to
Section 419-10
.
- If no DTCs related to the concern are retrieved, GO to
Symptom Chart - Engine Performance
.
Inspection and Verification — Engine NVH
- Engine NVH symptoms should be identified using the diagnostic tools and techniques that are available. For a list of these techniques, tools, an explanation of their uses and a glossary of common terms, refer to
Section 100-04
.
- Verify the customer concern by operating the engine to duplicate the condition.
- Inspect the engine for installation of an aftermarket oil filter. Review oil and filter maintenance history to make sure that the vehicle has not gone beyond the standard Ford recommended oil change interval.
- Check the engine oil level and check the oil for contamination. Low engine oil level or contaminated oil are common causes of engine noise. If the oil is contaminated, the source of the contamination must be identified and repaired as necessary.
- Visually inspect for obvious signs of mechanical damage. Refer to the following chart.
Visual Inspection Chart
Mechanical
|
---|
- Loose mounting bolts, studs and nuts
- Damaged or leaking powertrain mounts
- Damaged or disconnected vacuum hoses
- Damaged or disconnected air intake components
- Obstruction of cooling fan
- Obstruction of Front End Accessory Drive (FEAD)
- Obstruction of Rear End Accessory Drive (READ), if equipped
|
- If the inspection reveals obvious concerns that can be readily identified, repair as necessary.
NOTE:
Make sure to use the latest scan tool software release.
If the cause is not visually evident, connect the scan tool to the Data Link Connector (DLC).
NOTE:
The Vehicle Communication Module (VCM) LED prove out confirms power and ground from the
are provided to the
.
If the scan tool does not communicate with the
:
- check the
connection to the vehicle.
- check the scan tool connection to the
.
- refer to
Section 418-00
, No Power To The Scan Tool, to diagnose no power to the scan tool.
- If the scan tool does not communicate with the vehicle:
- verify the ignition key is in the ON position.
- verify the scan tool operation with a known good vehicle.
- Carry out the network test.
- If the scan tool responds with no communication for one or more modules, refer to
Section 418-00
.
- If the network test passes, retrieve and record
.
- Clear the
and carry out the self-test diagnostics for the PCM.
- If the DTCs retrieved are related to the concern, refer to
Section 419-10
.
- If no DTCs related to the concern are retrieved, continue the inspection and verification if a noise concern is related to the engine. For vibration concerns and noise concerns such as powertrain mounts, air intake system and starter GO to
Symptom Chart - Engine NVH
.
In some cases, a noise may be a normal characteristic of that engine type. In other cases the noise may require further investigation. Comparing the noise to a similar year/model vehicle equipped with the same engine will aid in determining if the noise is normal or abnormal.
Once a customer concern has been identified as an abnormal engine noise, it is critical to determine the location of the specific noise. Use the EngineEAR/ChassisEAR or stethoscope (the noise will always be louder closer to the noise source) to isolate the location of the noise to one of the following areas.
- Upper end of engine
- Lower end of engine
- Front of engine
- Rear of engine
Upper end engine noise
Common sources of upper end engine noise (ticking, knocking or rattle) include the fuel injectors, camshaft phaser sprocket(s), camshaft(s) and valve train. Upper end engine noise can be determined using the EngineEAR/ChassisEAR or stethoscope on the valve cover bolts. If the noise is loudest from the valve cover bolts, then the noise is upper end. The EngineEAR/ChassisEAR or stethoscope can be used to further isolate the noise to the specific cylinder bank and cylinder. Removal of the valve covers will be required to pinpoint the source of the noise.
- Fuel Injector Noise
- A common source of an engine ticking noise can be related to the fuel injector(s). This is normal engine noise that can be verified by listening to another vehicle. If the injector noise is excessive or irregular, use the EngineEAR/ChassisEAR or stethoscope to isolate the noise to a specific fuel injector.
- Valve Train
- Lash adjusters can make an engine ticking or tapping noise noticeable at any engine rpm or temperature and is audible through the wheel well or an open hood. However, with the hood down, lash adjuster noise can be heard as a light tapping noise through the wheel well and is considered normal. The EngineEAR/ChassisEAR or stethoscope can be used to further isolate the noise to the specific cylinder bank and cylinder, some disassembly of the engine may be required to inspect for damage or wear.
Lower end engine noise
A common source of lower end engine noise (ticking or knocking) include the crankshaft, connecting rod(s) and bearings. Lower end noises can be determined by using the oil pan or cylinder block lug bosses. If the noise is loudest from these areas then the noise is lower end. If an engine noise is isolated to the lower end, some disassembly of the engine may be required to inspect for damage or wear.
Front of engine noise
A common source of noise from the front of the engine (squeal, chirp, whine or hoot) is the Front End Accessory Drive (FEAD) components. To isolate
noise, carry out the Engine Accessory Test, refer to
Section 100-04
.
Some other noises from the front of the engine (ticking, tapping or rattle) may be internal to the engine. Use the EngineEAR/ChassisEAR or stethoscope on the engine front cover to determine if the noise is internal to the engine. Removal of the engine front cover may be necessary to inspect internal engine components.
Rear of engine noise
A common source of noise from the rear of the engine (knocking) is the flywheel/flexplate. Inspection of the flywheel/flexplate will be necessary.
- After the noise is localized, note the characteristics of the noise, including type of noise, frequency and conditions when the noise occurs and GO to
Symptom Chart - Engine NVH
.
Symptom Chart — Engine Performance
Symptom Chart — Engine NVH
Symptom Chart — Engine NVH
NOTE:
NVH symptoms should be identified using the diagnostic tools that are available. For a list of these tools, an explanation of their uses and a glossary of common terms, refer to
Section 100-04
. Since it is possible that any one of multiple systems may be the cause of the symptom, it may be necessary to use a process of elimination type of diagnostic approach to pinpoint the responsible system. If this is not the causal system for the symptom, refer back to
Section 100-04
for the next likely system and continue diagnosis.
Condition
| Possible Sources
| Action
|
| | |
- Drumming noise — occurs inside the vehicle during idle or high idle, hot or cold. Very low-frequency drumming is very rpm dependent
| - Engine vibration excites the body resonances inducing interior noise
| |
- Engine drumming noise — accompanied by vibration
| | |
- Rattle — occurs at idle or at light acceleration from a stop
| | - CHECK the powertrain mounts for damage. INSTALL new mounts as necessary. For engine, Refer to the appropriate section in Group
303
for the procedure. For automatic transmission, Refer to the appropriate section in Group
307
for the procedure.
|
- Whine/moan type noise — pitch increases or changes with vehicle speed
| | - CHECK the powertrain mounts for damage. INSTALL new mounts as necessary. For engine, Refer to the appropriate section in Group
303
for the procedure. For automatic transmission, Refer to the appropriate section in Group
307
for the procedure.
|
- Clunk — occurs when shifting from PARK or between REVERSE and DRIVE
| | - CHECK the powertrain/drivetrain mounts for damage. INSTALL new mounts as necessary. For engine, Refer to the appropriate section in Group
303
for the procedure. For automatic transmission, Refer to the appropriate section in Group
307
for the procedure.
|
| | - CHECK for the correct idle speed.
|
- Accessory drive bearing hoot — occurs at idle or high idle in cold temperatures of approximately +4°C (+40°F) or colder at the first start of the day
| - Accessory drive idler or tensioner pulley bearing is experiencing stick/slip between ball bearings and the bearing race
| - CARRY OUT the engine cold soak procedure. REFER to
Section 100-04
.
- PLACE the EngineEAR probe directly on the idler/tensioner center post or bolt to verify which bearing is making the noise. INSTALL new parts as necessary. Refer to the appropriate section in Group
303
for the procedure.
|
- Accessory drive belt noise, squeal or chirping
| - Defective/worn or incorrect accessory drive belt
- Misaligned pulley(s)
- Pulley runout
- Damaged or worn accessory drive component or idler
- Fluid contamination of the accessory drive belt or pulleys
- Damaged or worn accessory drive belt tensioner
- Damaged pulley grooves
| - CARRY OUT the Engine Accessory Test. REFER to
Section 100-04
. INSPECT components and INSTALL new parts as necessary. Refer to the appropriate section in Group
303
for the procedure.
|
| - Coolant pump has excessive end play or imbalance
| - CHECK the coolant pump for excessive end play. INSPECT the coolant pump for imbalance with the drive belt off. INSTALL a new coolant pump as necessary. Refer to the appropriate section in Group
303
for the procedure.
|
| | - CHECK the air cleaner and ducts for correct fit. INSPECT the air intake system for leaks or damage. REPAIR as necessary.Refer to the appropriate section in Group
303
for the procedure.
|
- Whistling noise — normally accompanied with poor idle condition
| | - CHECK the air intake ducts, Air Cleaner (ACL), Throttle Body (TB) and vacuum hoses for leaks and correct fit. REPAIR or ADJUST as necessary.Refer to the appropriate section in Group
303
for the procedure.
|
- Hissing noise — occurs during idle or high idle that is apparent with the hood open
| | - USE the EngineEAR to locate the source. SCAN the air intake system from the inlet to each cylinder intake port. DISCARD the leaking parts, and INSTALL a new component.
|
| - Vehicles with a plastic intake manifold
| - Acceptable condition. Some plastic manifolds exhibit this noise, which is the effect of the plastic manifold.
|
- Grinding noise — occurs during engine cranking
| - Incorrect starter motor mounting
| - INSPECT the starter motor for correct mounting. REPAIR as necessary. Refer to the appropriate section in Group
303
for the procedure.
|
| | - CHECK the starter motor. INSTALL a new starter motor as necessary. Refer to the appropriate section in Group
303
for the procedure.
|
| - Incorrect starter motor drive engagement
| - INSPECT the starter motor drive for wear or damage. INSTALL a new starter motor as necessary. Refer to the appropriate section in Group
303
for the procedure.
- INSPECT the flywheel/flexplate for wear or damage. INSTALL a new flywheel/flexplate as necessary. Refer to the appropriate section in Group
303
for the procedure.
|
- Engine noise, front of engine — knocking noise from lower front of engine
| - Damaged or separated crankshaft pulley/damper
| - CHECK for obvious signs of damage or wobble during operation. INSTALL new as necessary. Refer to the appropriate section in Group
303
for the procedure.
|
- Engine noise, front of engine — ticking, tapping or rattling noise from the front of the engine
| | - REMOVE the accessory drive belt. Refer to the appropriate section in Group
303
for the procedure.
- USE the EngineEAR to isolate the noise to the engine front cover.
- REMOVE the engine front cover and INSPECT the timing drive components. INSTALL new parts as necessary. Refer to the appropriate section in Group
303
for the procedure.
|
- Engine noise, upper end — ticking noise near the fuel rail and intake manifold
| | - CHECK for loose or damaged fuel rail clip(s). REPAIR as necessary. Refer to the appropriate section in Group
303
for the procedure.
|
| | - USE the EngineEAR to isolate the noisy injector(s). INSTALL new injector(s) as necessary. Refer to the appropriate section in Group
303
for the procedure.
|
- Engine noise, upper end — ticking, knocking or rattle noise that occurs during idle or high idle during the first cold start of the day and may disappear as the engine warms
| - Valve train noise (bled down lifter/lash adjuster)
| - CARRY OUT the Valve Train Analysis Component Test in this section. INSTALL new parts as necessary. Refer to the appropriate section in Group
303
for the procedure.
|
- Engine noise, upper end — occurs mostly with a warm engine at light/medium acceleration
| - Worn or damaged spark plugs
| - REMOVE the spark plugs. INSPECT and INSTALL new as necessary. Refer to the appropriate section in Group
303
for the procedure.
|
| - Carbon accumulation in combustion chamber
| - INSPECT the cylinder using a Bore scope. ELIMINATE carbon buildup.
|
- Engine noise, upper end — rattling noise from the valve train. Worse when the engine is cold
| | - CHECK the oil level. FILL as necessary.
|
| - Worn valve train components
| - CARRY OUT the Valve Train Analysis Component Test in this section. INSTALL new parts as necessary. Refer to the appropriate section in Group
303
for the procedure.
|
| | |
| - Excessive runout of the valve seats on the valve face
| |
- Engine noise, upper end — pinging noise
| | - VERIFY with customer the type of gasoline used. CORRECT as necessary.
|
| - Knock Sensor (KS) operation
| - CHECK the
. INSTALL a new
as necessary. Refer to the appropriate section in Group
303
for the procedure.
|
| | - REFER to the Powertrain Control/Emissions Diagnosis (PC/ED) manual.
|
| - High operating temperature
| - INSPECT the cooling system for leaks. CHECK the coolant level. REFILL as necessary. CHECK the coolant for the correct mix ratio. DRAIN and REFILL as needed. VERIFY the engine operating temperature is within specifications. REPAIR as necessary. Refer to the appropriate section in Group
303
for the procedure.
|
| | - CHECK the spark plugs. REPAIR or INSTALL new spark plugs as necessary. Refer to the appropriate section in Group
303
for the procedure.
|
| | |
- Engine noise, upper end — knocking or ticking noise, occurs mostly with a warm engine at idle
| | - CHECK the oil level. FILL as necessary.
|
| | - INSPECT the oil for contamination. If the oil is contaminated, CHECK for the source. REPAIR as necessary. CHANGE the oil and filter.
|
| - Damaged or incorrect oil filter
| - INSPECT the oil filter. INSTALL a new oil filter as necessary.
|
| | - CARRY OUT the oil pressure test.
|
- Engine noise, lower end — ticking or knocking noise near the oil filter adapter
| | - USE the EngineEAR to verify the oil pump as the source of the noise at low rpm. REPAIR as necessary. Refer to the appropriate section in Group
303
for the procedure.
|
- Engine noise, lower end — light knocking noise, also described as piston slap. Noise is most noticeable when the engine is cold with light to medium acceleration. The noise disappears as the engine warms
| - Excessive clearance between the piston and the cylinder wall
| |
- Engine noise, lower end — light double knock or sharp rap sound. Occurs mostly with a warm engine at idle or low speeds in drive. Increases in relation to engine load. Associated with a poor lubrication history
| - Excessive clearance between the piston and the piston pin
| |
- Engine noise, lower end — light knocking noise. The noise is most noticeable when the engine is warm. The noise tends to decrease when the vehicle is coasting or in NEUTRAL
| - Excessive clearance between the connecting rod bearings and the crankshaft
| |
- Engine noise, lower end — deep knocking noise. The noise is most noticeable when the engine is warm, at lower rpm and under a light load and then at float
| - Worn or damaged crankshaft main bearings
| |
- Engine noise, rear of engine — knocking noise at rear of engine
| - Damaged flywheel/flexplate
| |
- Engine vibration — vibration felt at all times
| - Excessive crankshaft pulley runout
| - CARRY OUT the Engine Accessory Test. INSTALL a new crankshaft pulley as necessary. Refer to the appropriate section in Group
303
for the procedure.
|
| - Damaged or worn accessory component
| - CARRY OUT the Engine Accessory Test. REPAIR or INSTALL a new component as necessary.
|
- Engine vibration — at idle, a low-frequency vibration (5-20 Hz) or mild shake that is felt through the seat/floorpan
| | - Using the scan tool, CARRY OUT the cylinder power balance and the relative compression test. REPAIR as necessary. Refer to the appropriate section in Group
303
for the procedure.
|
| - Engine or torque converter out of balance
| - VERIFY the torque converter to crankshaft pilot clearance is correct. REPAIR as necessary. RE-INDEX the torque converter on the flexplate by 120 degrees for a 3-bolt converter or 180 degrees for a 4-bolt converter. Refer to the appropriate section in Group
307
for the procedure.
|
- Engine vibration — is felt with increases and decreases in engine rpm
| | - CHECK the powertrain mounts for damage. INSTALL new mounts as necessary. For engine, Refer to the appropriate section in Group
303
for the procedure. For automatic transmission, Refer to the appropriate section in Group
307
for the procedure.
|
| - Engine or transmission contacting the chassis
| - INSPECT the powertrain/drivetrain for correct clearances. REPAIR as necessary.
|
- Engine vibration — increases intensity as the engine rpm is increased
| | - CARRY OUT the Neutral Engine Run-Up (NERU) Test. REFER to
Section 100-04
. ROTATE the torque converter, 120 degrees for 3-bolt or 180 degrees for 4-bolt. INSPECT the torque converter pilot outer diameter to crankshaft pilot inner diameter. REPAIR as necessary. Refer to the appropriate section in Group
307
for the procedure.
|
- Engine vibration — mostly at coast/neutral coast. Condition improves with vehicle acceleration
| | - CHECK the ignition system. INSTALL new components as necessary. Refer to the appropriate section in Group
303
for the procedure.
|
- Engine vibration or shudder — occurs with light to medium acceleration above 56 km/h (35 mph)
| - Worn or damaged spark plugs
| - INSPECT the spark plugs for cracks, high resistance or broken insulators. INSTALL a new spark plug(s) as necessary. Refer to the appropriate section in Group
303
for the procedure.
|
| | - INSTALL a new fuel injector as necessary. Refer to the appropriate section in Group
303
for the procedure.
|
| | - INSPECT the fuel for contamination. DRAIN the fuel system and refill.
|
Pinpoint Tests
Pinpoint Test A: Low Oil Pressure
Normal Operation
Oil is drawn into the oil pump through the oil pump screen and pickup tube in the sump of the oil pan. Oil is pumped through the oil filter on the left front side of the cylinder block then enters the main gallery where it is distributed to the crankshaft main journals and to both cylinder heads. From the main journals, the oil is routed through cross-drilled passages in the crankshaft to lubricate the connecting rod bearings. Controlled leakage through the crankshaft main bearings and connecting rod bearings is slung radially outward to cool and lubricate the cylinder walls as well as the entire connecting rod, piston and piston ring assembly. The left cylinder head is fed from a drilling into the supply passage feeding the main gallery at the front of the cylinder block. The right cylinder head is fed from a drilling into the rear of the main gallery. Main gallery pressure is reduced as it enters the cylinder head galleries through fixed serviceable orifices, located at the upper part of the feed passages. It is this reduced pressure in the cylinder head galleries which feed the camshaft journals, the hydraulic lash adjusters and the primary and secondary timing chain tensioners. The camshaft lobe and roller followers or rocker arms are lubricated by splash created through valve train operation.
This pinpoint test is intended to diagnose the following:
- Excessive crankshaft end play
- Excessive main bearing clearance
- Excessive connecting rod bearing clearance
- Excessive camshaft bearing cap clearance
- Loose oil galley plugs
- Loose timing chain tensioner bolts
- Oil pump screen and pickup tube
- Restricted oil flow passages
- Worn or damaged oil pump
PINPOINT TEST A: LOW OIL PRESSURE
Test Step
| Result / Action to Take
|
---|
A1 CHECK THE CRANKSHAFT END PLAY
|
|
- Check the crankshaft end play. Refer to
Crankshaft End Play
in this section.
- Is the crankshaft end play within specification?
| Yes
GO to
A2
.
No
REPAIR as necessary. Refer to the appropriate section in Group
303
for the procedure.
|
A2 VERIFY THE CAMSHAFT BEARING CAPS ARE NOT DAMAGED AND TIGHT
|
|
- Check that the camshaft bearing caps are not damaged and the bolts are properly tightened. Refer to the Specification chart in the appropriate engine section.
- Are the camshaft bearing caps loose or damaged?
| Yes
REPAIR as necessary. Refer to the appropriate section in Group
303
for the procedure.
No
GO to
A3
.
|
A3 CHECK CAMSHAFT JOURNAL-TO-BEARING CLEARANCE
|
|
- Check the camshaft journal-to-bearing clearance. Refer to the Specification chart in the appropriate engine section.
- Is camshaft journal-to-bearing clearance within specification?
| Yes
GO to
A4
.
No
REPAIR as necessary. Refer to the appropriate section in Group
303
for the procedure.
|
A4 CHECK FOR RESTRICTED OIL FLOW
|
|
- Verify the oil supply and return passages are not plugged and clean of debris. Refer to the oil flow chart in the appropriate engine section.
- Is oil flow restricted?
| Yes
REPAIR as necessary. Refer to the appropriate section in Group
303
for the procedure.
No
GO to
A5
.
|
A5 CHECK THE TIMING CHAIN TENSIONERS FOR DAMAGE AND VERIFY THE BOLTS ARE TIGHT
|
|
- Check that the timing chain tensioners are not damaged or the bolts are loose. Refer to the Specification chart in the appropriate engine section.
- Are the timing chain tensioners damaged or bolts loose?
| Yes
REPAIR as necessary. Refer to the appropriate section in Group
303
for the procedure.
No
GO to
A6
.
|
A6 CHECK THE OIL PUMP PICKUP TUBE AND SCREEN FOR DAMAGE
|
|
- Check that the oil pump pickup tube and screen is not plugged, cracked or that the bolts are loose. Refer to the Specification chart in the appropriate engine section.
- Is the oil pump screen and pickup tube damaged or loose?
| Yes
REPAIR as necessary. Refer to the appropriate section in Group
303
for the procedure.
No
GO to
A7
.
|
A7 CHECK THE OIL PUMP FOR DAMAGE
|
|
- Verify the oil pump is not damaged.
- Is oil pump damaged?
| Yes
REPAIR as necessary. Refer to the appropriate section in Group
303
for the procedure.
No
GO to
A8
.
|
A8 CHECK CRANKSHAFT MAIN BEARING JOURNAL-TO-BEARING CLEARANCE
|
|
- Check the crankshaft main bearing journal-to-bearing clearance. Refer to the Specification chart in the appropriate engine section.
- Is crankshaft main bearing journal-to-bearing clearance within specification?
| Yes
GO to
A9
.
No
REPAIR as necessary. Refer to the appropriate section in Group
303
for the procedure.
|
A9 CHECK CONNECTING ROD BEARING JOURNAL-TO-BEARING CLEARANCE
|
|
- Check the connecting rod bearing journal-to-bearing clearance. Refer to the Specification chart in the appropriate engine section.
- Is connecting rod bearing journal-to-bearing clearance within specification?
| Yes
The concern may have been caused by debris or an incorrect assembly. REPEAT the oil pressure test.
No
REPAIR as necessary. Refer to the appropriate section in Group
303
for the procedure.
|
Component Tests
The following component tests are used to diagnose engine concerns.
Engine Oil Leaks
NOTICE:
If an overnight drive is done, the fan air or road air blast may cause erroneous readings.
NOTE:
When diagnosing engine oil leaks, the source and location of the leak must be positively identified prior to repair.
Prior to carrying out this procedure, clean the cylinder block, cylinder heads, valve covers, oil pan and flywheel with a suitable solvent to remove all traces of oil.
Engine Oil Leaks — Fluorescent Oil Additive Method
Use the 12 Volt Master UV Diagnostic Inspection Kit to carry out the following procedure for oil leak diagnosis.
- Add 29.6 ml (1 oz) of gasoline engine oil dye to a minimum of 0.47L (1/2 qt) and a maximum of 0.95L (1 qt) engine oil and fill through the engine oil fill. If the oil is not premixed, the gasoline engine oil dye will not have enough time to reach the crankcase, oil galleries and seal surfaces during this particular 15 minute test. The gasoline engine oil dye must be mixed with oil and added through the oil fill. Check the level on the oil level indicator to determine what amount of oil to premix. If it is in the middle of the crosshatch area or below the full mark, use 0.95L (1 qt). If it is at the full mark, use 0.47L (1/2 qt).
- Run the engine for 15 minutes. Stop the engine and inspect all seal and gasket areas for leaks using the UV Diagnostic Inspection Kit. A clear bright yellow or orange area will identify the leak. For extremely small leaks, several hours may be required for the leak to appear.
- At the end of test, make sure the oil level is within the upper and lower oil indicator marks. Remove oil as necessary if it registers above the full mark.
Leakage Points — Underhood
Examine the following areas for oil leakage:
- Valve cover gaskets
- Cylinder head gaskets
- Oil cooler, if equipped
- Oil filter adapter
- Engine front cover
- Oil filter adapter and filter body
- Oil level indicator tube connection
- Engine Oil Pressure (EOP) sensor
- Oil passage end plugs
Leakage Points — Under Engine, With Vehicle on Hoist
Examine the following areas for oil leakage:
- Oil pan gaskets
- Oil pan sealer
- Engine front cover gasket
- Crankshaft front seal
- Crankshaft rear oil seal
- Oil filter adapter and filter body
- Oil cooler, if equipped
- Oil passage end plugs
Leakage Points — With Transmission and Flywheel Removed
Examine the following areas for oil leakage:
- Crankshaft rear seal
- Crankshaft rear seal retainer
- Rear main bearing cap parting line — 5.8L (4V) engines
- Flexplate mounting bolt holes (with flexplate installed)
- Oil passage end plugs
Oil leaks at crimped seams in sheet metal parts and cracks in cast or stamped parts can be detected when using the Gasoline Engine Oil Dye method.
Compression Test — Compression Gauge Check
- Make sure the oil in the crankcase is of the correct viscosity and at the correct level and that the battery is correctly charged. Operate the vehicle until the engine is at normal operating temperature. Turn the ignition switch to the OFF position, then remove all the spark plugs.
- Set the throttle plates in the wide-open position.
- Install a compression gauge in the No. 1 cylinder.
- Install an auxiliary starter switch in the starting circuit. With the ignition switch in the OFF position, and using the auxiliary starter switch, crank the engine a minimum of 5 compression strokes and record the highest reading. Note the approximate number of compression strokes required to obtain the highest reading.
- Repeat the test on each cylinder, cranking the engine approximately the same number of compression strokes.
Compression Test — Test Results
The indicated compression pressures are considered within specification if the lowest reading cylinder is at least 75% of the highest reading. Refer to the Compression Pressure Limit Chart.
Compression Pressure Limit Chart
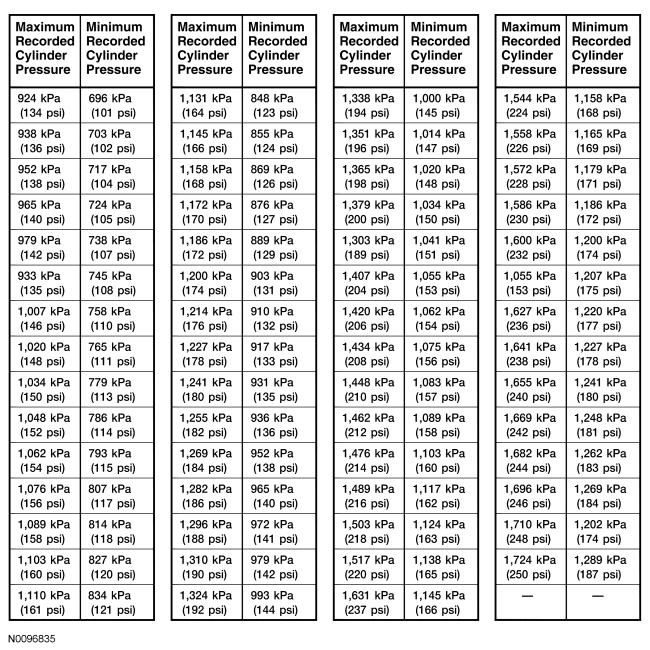
If one or more cylinders reads low, squirt approximately one tablespoon of engine oil on top of the pistons in the low-reading cylinders. Repeat the compression pressure check on these cylinders.
Compression Test — Interpreting Compression Readings
- If compression improves considerably, piston rings are faulty.
- If compression does not improve, valves are sticking or seating incorrectly.
- If 2 adjacent cylinders indicate low compression pressures and squirting oil on each piston does not increase compression, the head gasket may be leaking between cylinders. Engine oil or coolant in cylinders could result from this condition.
Use the Compression Pressure Limit Chart when checking cylinder compression so that the lowest reading is within 75% of the highest reading.
Cylinder Leakage Detection
When a cylinder produces a low reading, use of a cylinder leakage tester will be helpful in pinpointing the exact cause.
The leakage tester is inserted in the spark plug hole, the piston is brought up to dead center on the compression stroke and compressed air is admitted.
Once the combustion chamber is pressurized, the leakage tester gauge will read the percentage of leakage. Leakage exceeding 20% is excessive.
While the air pressure is retained in the cylinder, listen for the hiss of escaping air. A leak at the intake valve will be heard in the Throttle Body (TB). A leak at the exhaust valve can be heard at the tail pipe. Leakage past the piston rings will be audible at the PCV connection. If air is passing through a blown head gasket to an adjacent cylinder, the noise will be evident at the spark plug hole of the cylinder into which the air is leaking. Cracks in the cylinder block or gasket leakage into the cooling system may be detected by a stream of bubbles in the radiator.
Excessive Engine Oil Consumption
Nearly all engines consume oil, which is essential for normal lubrication of the cylinder bore walls and pistons and rings. Determining the level of oil consumption may require testing by recording how much oil is being added over a given set of miles.
Customer driving habits greatly influence oil consumption. Mileage accumulated during towing or heavy loading generates extra heat. Frequent short trips, stop-and-go type traffic or extensive idling, prevent the engine from reaching normal operating temperature. This prevents component clearances from reaching specified operating ranges.
The following diagnostic procedure may be utilized to determine internal oil consumption. Make sure that the concern is related to internal oil consumption, and not external leakage, which also consumes oil. Verify there are no leaks before carrying out the test. Once verified, the rate of internal oil consumption can be tested.
A new engine may require extra oil in the early stages of operation. Internal piston-to-bore clearances and sealing characteristics improve as the engine breaks in. Engines are designed for close tolerances and do not require break-in oils or additives. Use the oil specified in the Owner's Literature. Ambient temperatures may determine the oil viscosity specification. Verify that the correct oil is being used for the vehicle in the geographic region in which it is driven.
Basic Pre-checks
- For persistent complaints of oil consumption, interview the customer to determine the oil consumption characteristics. If possible, determine the brand and grade of oil currently in the oil pan. Look at the oil filter or oil-change station tags to determine if Ford-recommended maintenance schedules have been followed. Make sure that the oil has been changed at the specified mileage intervals. If vehicle mileage is past the first recommended drain interval, the OEM production filter should have been changed.
- Ask how the most current mileage was accumulated. That is, determine whether the vehicle was driven under the following conditions:
- Extended idling or curbside engine operation
- Stop-and-go traffic or taxi operation
- Towing a trailer or vehicle loaded heavily
- Frequent short trips (engine not up to normal operating temperature)
- Excessive throttling or high engine-rpm driving
- Verify that there are no external leaks. If necessary, review the diagnostic procedure under Engine Oil Leaks in the Diagnosis and Testing portion of this section.
- Inspect the crankcase ventilation system for:
- disconnected hoses at the valve cover or
.
- loose or missing valve cover fill cap.
- missing or incorrectly seated engine oil level indicator.
- incorrect or dirty PCV valve.
- a PCV valve grommet unseated in the valve cover (if so equipped).
- Inspect for signs of sludge. Sludge affects PCV performance and can plug or restrict cylinder head drainback wells. It can also increase oil pressure by restricting passages and reducing the drainback capability of piston oil control rings.
- Inspect the air filter for dirt, sludge or damage. A hole in the filter element will allow unfiltered air to bypass into the air induction system. This can cause premature internal wear (engine dusting), allowing oil to escape past rings, pistons, valves and guides.
- If the engine is hot or was recently shut down, wait at least 5 minutes to allow the oil to drain back. Ask the customer if this requirement has been followed. Adding oil without this wait period can cause an overfill condition, leading to excessive oil consumption and foaming which may cause engine damage.
- Make sure the oil level indicator (dipstick) is correctly and fully seated in the indicator tube. Remove the oil level indicator and record the oil level.
Detailed Pre-checks
- Check the thermostat opening temperature to make sure that the cooling system is operating at the specified temperature. If it is low, internal engine parts are not running at specified internal operating clearances.
- Verify the spark plugs are not oil saturated. Oil leaking into one or more cylinders will appear as an oil soaked condition on the plug. If a plug is saturated, a compression check may be necessary at the conclusion of the oil consumption test.
Oil Consumption Test
Once all of the previous conditions are met, carry out an oil consumption test.
- Drain the engine oil and remove the oil filter. Install a new manufacturer-specified oil filter. Make sure the vehicle is positioned on a level surface. Refill the oil pan to a level
1 liter (1 quart) less
than the specified fill level, using manufacturer-specified oil.
- Run the engine for 3 minutes (if hot) or 10 minutes (if cold). Allow for a minimum 5-minute drainback period and then record the oil level shown on the oil level indicator. Place a mark on the backside of the oil level indicator noting the oil level location.
- Add the final 1 L (1 qt) to complete the normal oil fill. Restart the engine and allow it to idle for 2 minutes. Shut the engine down.
- After a 5-minute drainback period, record the location of the oil level again. Mark the oil level indicator with the new oil level location. (Note: Both marks should be very close to the MIN-MAX upper and lower limits or the upper and lower holes on the oil level indicator. These marks will exactly measure the engine's use of oil, with a one quart differential between the new marks.) Demonstrate to the customer that the factory-calibrated marks on the oil level indicator are where the oil should fall after an oil change with the specified fill amount. Explain however, that this may vary slightly between MIN-MAX or the upper and lower holes on the oil level indicator.
- Record the vehicle mileage.
- Advise the customer that oil level indicator readings must be taken every 320 km (200 mi) or weekly, using the revised marks as drawn. Remind the customer that the engine needs a minimum 5-minute drainback for an accurate reading and that the oil level indicator must be firmly seated in the tube prior to taking the reading.
- When the subsequent indicator readings demonstrate a full quart (liter) has been used, record the vehicle mileage. The mileage driven between the 2 readings should not be less than 4,800 km (3,000 miles). The drive cycle the vehicle has been operated under must be considered when making this calculation. It may be necessary to have the customer bring the vehicle in for a periodic oil level indicator reading to closely monitor oil usage.
Post Checks, Evaluation and Corrective Action
- If test results indicate excessive oil consumption, carry out a cylinder compression test. The cylinder compression test should be carried out with a fully charged battery and all spark plugs removed. See the Compression Test Chart in this section for pressure range limits.
- Compression should be consistent across all cylinders. Refer to the Compression Testing portion of this section. If compression tested within the specifications found in this section, the excessive oil consumption may be due to wear on the valve guides, valves or valve seals.
- A cylinder leak detection test can be carried out using a cylinder leakage tester. This can help identify valves, piston rings, or worn valve guides/valve stems, inoperative valve stem seals or other related areas as the source of oil consumption.
NOTE:
An oil-soaked appearance on the porcelain tips of the spark plugs also indicates excessive oil use. A typical engine with normal oil consumption will exhibit a light tan to brown appearance. See Spark Plug Analysis in this section for details. A single or adjoining, multiple cylinder leak can be traced by viewing the tips.
- If an internal engine part is isolated as the root cause, determine if the repair will exceed cost limits and proceed with a repair strategy as required.
- Once corrective action to engine is complete and verifying that all pre-check items were eliminated in the original diagnosis, repeat the Oil Consumption Test as described above and verify consumption results.
Intake Manifold Vacuum Test
Bring the engine to normal operating temperature. Connect the Vacuum/Pressure Tester to the intake manifold. Run the engine at the specified idle speed.
The vacuum gauge should read between 51-74 kPa (15-22 in-Hg) depending upon the engine condition and the altitude at which the test is performed. Subtract 4.0193 kPa (1 in-Hg) from the specified reading for every 304.8 m (1,000 ft) of elevation above sea level.
The reading should be steady. If necessary, adjust the gauge damper control (where used) if the needle is fluttering rapidly. Adjust the damper until the needle moves easily without excessive flutter.
Intake Manifold Vacuum Test — Interpreting Vacuum Gauge Readings
A careful study of the vacuum gauge reading while the engine is idling will help pinpoint trouble areas. Always conduct other appropriate tests before arriving at a final diagnostic decision. Vacuum gauge readings, although helpful, must be interpreted carefully.
Most vacuum gauges have a normal band indicated on the gauge face.
The following are potential gauge readings. Some are normal; others should be investigated further.
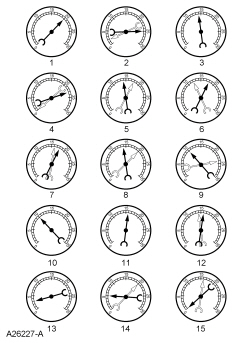
- NORMAL READING: Needle between 51-74 kPa (15-22 in-Hg) and holding steady.
- NORMAL READING DURING RAPID ACCELERATION AND DECELERATION: When the engine is rapidly accelerated (dotted needle), the needle will drop to a low reading (not to zero). When the throttle is suddenly released, the needle will snap back up to a higher than normal figure.
- NORMAL FOR HIGH-LIFT CAMSHAFT WITH LARGE OVERLAP: The needle will register as low as 51 kPa (15 in-Hg), but will be relatively steady. Some oscillation is normal.
- WORN RINGS OR DILUTED OIL: When the engine is accelerated (dotted needle), the needle drops to 0 kPa (0 in-Hg). Upon deceleration, the needle runs slightly above 74 kPa (22 in-Hg).
- STICKING VALVES: When the needle (dotted) remains steady at a normal vacuum, but occasionally flicks (sharp, fast movement) down and back about 13 kPa (4 in-Hg), one or more valves may be sticking.
- BURNED OR WARPED VALVES: A regular, evenly-spaced, downscale flicking of the needle indicates one or more burned or warped valves. Insufficient hydraulic lash adjuster or hydraulic lash adjuster clearance will also cause this reaction.
- POOR VALVE SEATING: A small but regular downscale flicking can mean one or more valves are not seating.
- WORN VALVE GUIDES: When the needle oscillates over about a 13 kPa (4 in-Hg) range at idle speed, the valve guides could be worn. As engine speed increases, the needle will become steady if guides are responsible.
- WEAK VALVE SPRINGS: When the needle oscillation becomes more violent as engine rpm is increased, weak valve springs are indicated. The reading at idle could be relatively steady.
- LATE VALVE TIMING: A steady but low reading could be caused by late valve timing.
- IGNITION TIMING RETARDING: Retarded ignition timing will produce a steady, but somewhat low, reading.
- INSUFFICIENT SPARK PLUG GAP: When spark plugs are gapped too close, a regular, small pulsation of the needle can occur.
- INTAKE LEAK: A low, steady reading can be caused by an intake manifold or throttle body gasket leak.
- BLOWN HEAD GASKET: A regular drop of fair magnitude can be caused by a blown head gasket or warped cylinder head-to-cylinder block surface.
- RESTRICTED EXHAUST SYSTEM: When the engine is first started and is idled, the reading may be normal, but as the engine rpm is increased, the back pressure caused by a clogged muffler, kinked tail pipe or other concerns will cause the needle to slowly drop to 0 kPa (0 in-Hg). The needle then may slowly rise. Excessive exhaust clogging will cause the needle to drop to a low point even if the engine is only idling.
- When vacuum leaks are indicated, search out and correct the cause. Excess air leaking into the system will upset the fuel mixture and cause concerns such as rough idle, missing on acceleration or burned valves. If the leak exists in an accessory unit such as the power brake booster, the unit will not function correctly. Always fix vacuum leaks.
Oil Pressure Test
NOTICE:
Inspect the engine for installation of an aftermarket oil filter. Review oil and filter maintenance history to make sure that the vehicle has not gone beyond the standard Ford recommended oil change intervals. Check the engine oil level and check the oil for contamination. If the oil is contaminated, engine damage can occur. The source of the contamination must be identified and repaired as necessary.
- Disconnect and remove the Engine Oil Pressure (EOP) switch from the engine. Refer to the appropriate section in Group
303
for the procedure.
- Connect the Oil Pressure Gauge to the oil pressure port.
- Run the engine until normal operating temperature is reached.
- With the engine at idle record the gauge reading.
- Run the engine at 2,000 rpm and record the gauge reading.
- The oil pressure should be within specifications; refer to the specifications in the appropriate engine section.
- If the pressure is not within specification,
GO to Pinpoint Test A
.
Valve Train Analysis — 3.7L Engines
The following component tests are used to diagnose valve train concerns.
Valve Train Analysis — Engine Off, Valve Cover Removed
Check for damaged or severely worn parts and correct assembly. Make sure correct parts are used with the static engine analysis as follows.
Valve Train Analysis — Camshafts and Valve Tappets
- Check for broken or damaged parts.
- Check for loose mounting bolts on camshaft caps.
- Check for worn or damaged valve tappets.
Valve Train Analysis — Valve Springs, Valve Tappets Removed
- Check for broken or damaged parts.
Valve Train Analysis — Valve Spring Retainer and Valve Spring Retainer Keys, Valve Tappets Removed
- Check for correct seating of the valve spring retainer key on the valve stem and in valve spring retainer.
- Check for correct seating on the valve stem.
Valve Train Analysis — Valves and Cylinder Head, Valve Tappets Removed
- Check for plugged oil drain-back holes.
- Check for worn or damaged valve tips.
- Check for missing or damaged valve stem seals or guide-mounted valve stem seal.
- Check for missing or worn valve spring seats.
Valve Train Analysis — Camshaft Lobe Lift
Check the lift of each camshaft lobe in consecutive order and make a note of the readings.
- Remove the spark plugs. Refer to
Section 303-07A
.
- Install the Dial Indicator Gauge with Holding Fixture so the rounded tip of the dial indicator is on top of the camshaft lobe and on the same plane as the valve tappet.
- Rotate the crankshaft using a breaker bar and socket attached to the crankshaft pulley retainer bolt. Rotate the crankshaft until the base circle of the camshaft lobe is reached.
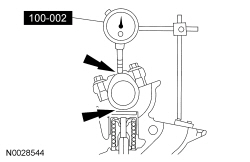
- Zero the dial indicator. Continue to rotate the crankshaft until the high-lift point of the camshaft lobe is in the fully-raised position (highest indicator reading).
- To check the accuracy of the original dial indicator reading, continue to rotate crankshaft until the base circle is reached. The dial indicator reading should be zero. If zero reading is not obtained, repeat Steps 1 through 6.
- If the lift on any lobe is below specified service limits, install a new camshaft and camshaft valve tappets.
- Install the spark plugs. Refer to
Section 303-07A
.
Valve Train Analysis — 5.0L and 5.8L (4V) Engines
The following component tests are used to diagnose valve train concerns.
Valve Train Analysis — Engine Off — Valve Cover Removed
Check for damaged or severely worn parts and correct assembly. Make sure correct parts are used with the static engine analysis as follows.
Valve Train Analysis — Engine Off, Camshaft Roller Followers and Hydraulic Lash Adjusters, Overhead Camshaft
- Check for loose mounting bolts on camshaft carriers.
- Check for plugged oil feed in the camshaft roller followers, lash adjusters or cylinder heads.
Valve Train Analysis — Engine Off, Camshaft — Engines
- Check for broken or damaged parts.
Valve Train Analysis — Valve Springs
- Check for broken or damaged parts.
Valve Train Analysis — Engine Off, Valve Spring Retainer and Valve Spring Retainer Keys
- Check for correct seating of the valve spring retainer key on the valve stem and in valve spring retainer.
- Check for correct seating on the valve stem.
Valve Train Analysis — Engine Off, Valves and Cylinder Head
- Check for plugged oil drain back holes.
- Check for worn or damaged valve tips.
- Check for missing or damaged guide-mounted valve stem seal.
- Check for damaged hydraulic lash adjuster.
- Check installed valve spring height.
- Check for missing or worn valve spring seats.
- Check for plugged oil metering orifice in cylinder head oil reservoir (if equipped).
Static checks (engine off) are to be made on the engine prior to the dynamic procedure.
Valve Train Analysis — Engine Running, Valves and Cylinder Head
- Check for plugged oil drain back holes.
- Check for missing or damaged valve stem seals or guide mounted valve stem seals.
- Check for a plugged oil metering orifice in the cylinder head oil reservoir.
If insufficient oiling is suspected, check oil passages for blockage, then accelerate the engine to 1,200 rpm with the transmission in NEUTRAL and the engine at normal operating temperature. Oil should spurt from the rocker arm oil holes such that valve tips and camshaft roller followers are well oiled. With the valve covers off, some oil splash may overshoot camshaft roller followers.
Valve Train Analysis — Camshaft Lobe Lift
Check the lift of each camshaft lobe in consecutive order and make a note of the readings.
- Remove the spark plugs. Refer to
Section 303-07B
for 5.0L engines or
Section 303-07C
for 5.8L (4V) engines.
- Install the Dial Indicator Gauge with Holding Fixture so the rounded tip of indicator is on top of the camshaft lobe.
- Rotate the crankshaft using a breaker bar and socket attached to the crankshaft pulley retainer bolt. Rotate the crankshaft until the base circle of the camshaft lobe is reached.
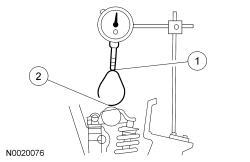
- Zero the Dial Indicator Gauge. Continue to rotate the crankshaft until the (1) high-lift point of the camshaft lobe is in the fully-raised position (highest indicator reading).
- To check the accuracy of the original indicator reading, continue to rotate crankshaft until the (2) base circle is reached. The indicator reading should be zero. If zero reading is not obtained, repeat the measurement.
- If the lift on any lobe is below specified service limits, install a new camshaft and camshaft roller followers.
- Install the spark plugs. Refer to
Section 303-07B
for 5.0L engines or
Section 303-07C
for 5.8L (4V) engines.